Introduction to Automotive Side Impact Protection
In modern automotive engineering, occupant safety is paramount, with impact beam in cars serving as crucial structural elements specifically designed to protect passengers during collisions. These specialized components, known technically as side intrusion beams or side impact bars, form a reinforced skeletal structure within vehicle doors and frames. Side impact bars in cars are strategically positioned to absorb and dissipate kinetic energy during crashes, creating a critical safety buffer between occupants and potential intrusion points. This article provides an exhaustive analysis of the engineering principles, material science, and evolving standards governing these vital safety components.
Safety Statistics Highlighting Importance
According to IIHS data, side-impact collisions account for approximately 24% of passenger vehicle occupant fatalities. Vehicles equipped with advanced side impact protection bar systems show a 31% reduction in serious thoracic injuries. NHTSA research further confirms that optimized door beam systems can decrease intrusion by 52% in 50km/h collision scenarios.
Industry Trends in Side Impact Protection
The automotive safety sector is experiencing rapid transformation driven by technological innovation and regulatory evolution:
Material Science Revolution
Traditional mild steel (200-350 MPa yield strength) has been replaced by advanced high-strength steels (AHSS) with 500-1500 MPa strength. Hot-stamped boron steels have become the gold standard for side intrusion beams, offering exceptional strength-to-weight ratios. The latest innovations include aluminum alloys and carbon fiber composites, enabling 40% weight reduction without compromising protection levels.
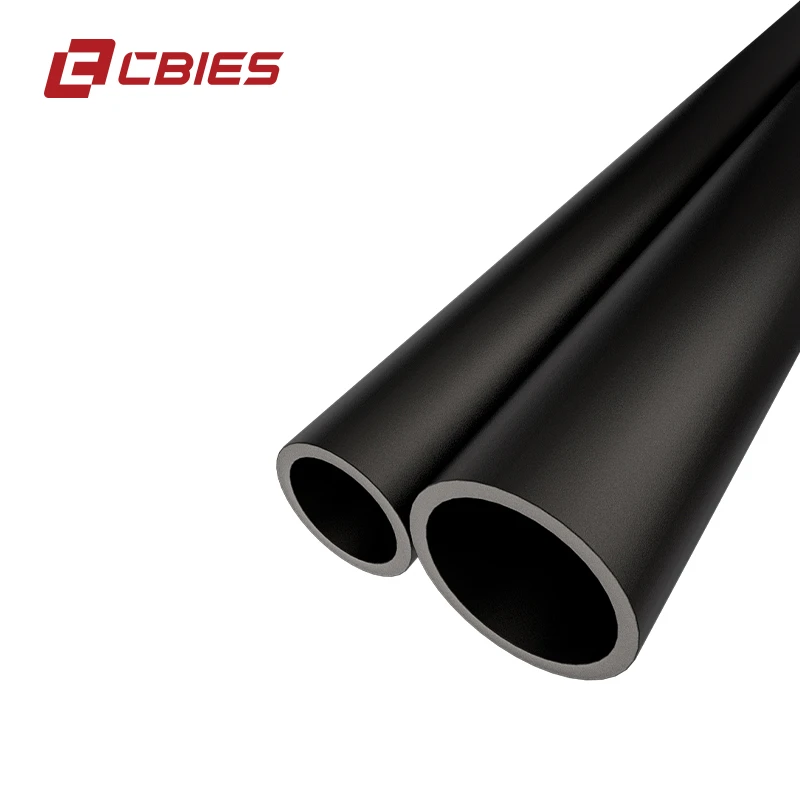
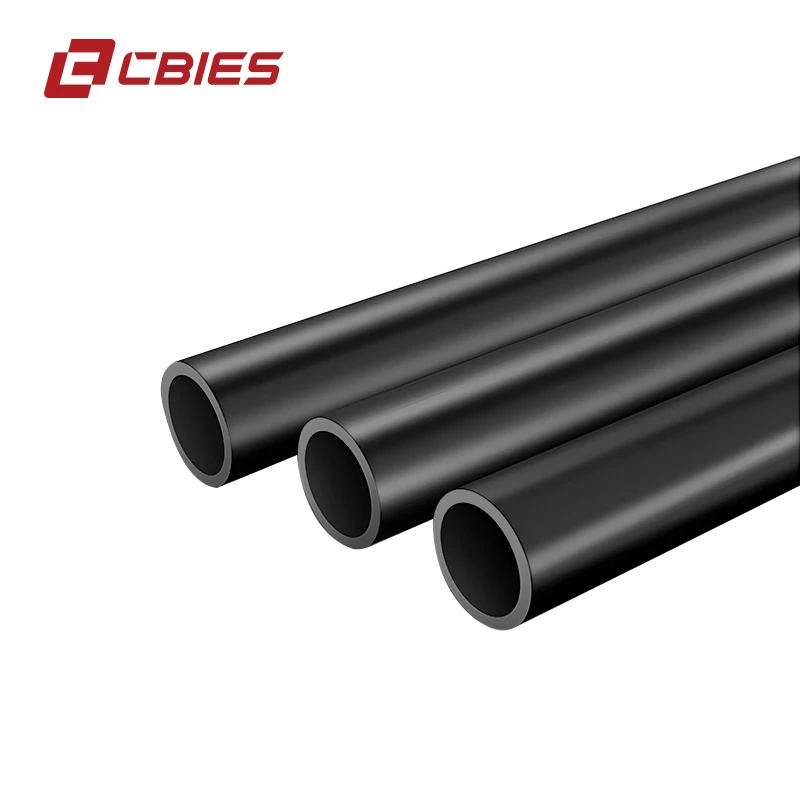
Regulatory Evolution
Global safety standards are continually being updated to address real-world collision scenarios. The latest Euro NCAP protocols introduced oblique pole tests (32km/h at 75° angle) to evaluate side impact bars performance. Similarly, IIHS recently implemented enhanced side-test evaluations incorporating heavier, higher-riding impactors to simulate modern SUV collisions.
Integration with Active Safety Systems
Modern impact beam in cars are increasingly integrated with predictive safety systems. BMW's latest models feature sensors that detect impending collisions, triggering pre-tensioning mechanisms in door reinforcement systems 150 milliseconds before impact, optimizing the structural response of side impact protection bar configurations.
Technical Parameters of Modern Impact Beams
Parameter | Industry Standard | Advanced Performance | Measurement Protocol |
---|---|---|---|
Tensile Strength | 800-1000 MPa | 1500-2000 MPa | ISO 6892-1 |
Yield Strength | 500-700 MPa | 1200-1400 MPa | ASTM E8/E8M |
Energy Absorption | 15-20 kJ | 30-45 kJ | SAE J211 Crash Test |
Maximum Intrusion | ≤300mm | ≤150mm | FMVSS 214 Compliance |
Weight Efficiency | 1.2-1.8 kg/m | 0.6-1.0 kg/m | Component Density Ratio |
Bending Moment | 5-7 kN-m | 10-14 kN-m | Three-Point Bend Test |
Corrosion Resistance | 500 hours salt spray | 1000+ hours | ASTM B117 |
Material Engineering Breakthroughs
The latest generation of side impact bars in cars utilizes press-hardened steels with tailored properties through differential heat treatment. This creates strategic soft zones (approximately 20% of beam length) that control deformation patterns and increase energy absorption capacity by 40% compared to homogeneous designs. Advanced finite element analysis enables engineers to optimize geometries beyond traditional circular and octagonal sections to include hybrid trapezoidal designs.
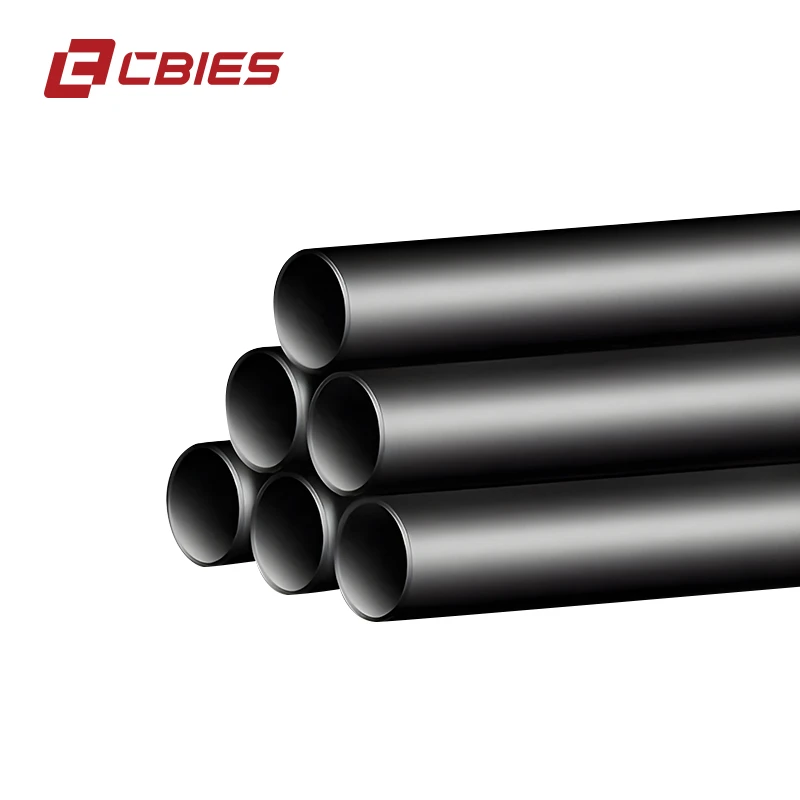
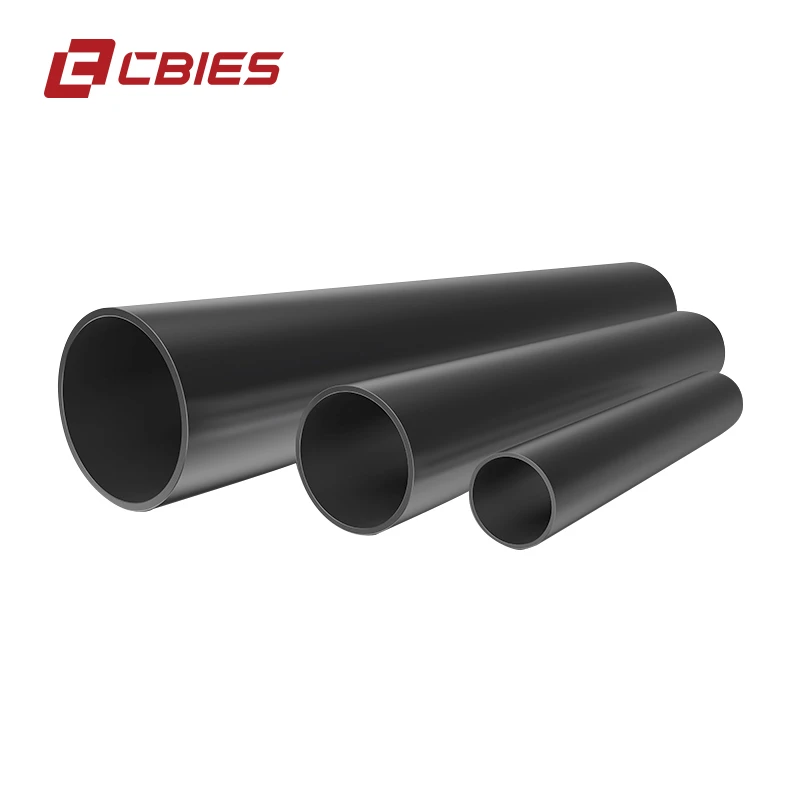
CBIES Door Impact Beam Tube: Premium Protection System
HEBEI CBIES AUTOMOTIVE PARTS CO., LTD. engineers advanced Door Impact Beam Tube solutions that exceed international safety standards. Our precision-engineered impact beam in cars provide exceptional occupant protection while optimizing vehicle weight distribution.
Technical Specifications
- Material: Boron-alloyed steel (1500 MPa tensile strength)
- Energy Absorption Capacity: 38-42 kJ (depending on configuration)
- Corrosion Protection: Triple-layer zinc-nickel electrocoating
- Temperature Range: -50°C to +180°C operational stability
- Compliance: FMVSS 214, ECE R95, GB 15743 standards
Installation Mechanics and Vehicle Integration
Optimizing the effectiveness of side intrusion beams requires sophisticated integration strategies:
Structural Interface Engineering
Advanced beam systems feature adaptive mounting brackets with crash-initiated deformation controllers. These elements absorb 30-45% of impact energy before the main side impact bars engage, creating a staged energy management system that reduces peak forces on occupants by up to 60%.
Positioning Precision
Current industry best practices position the primary side impact protection bar 300-400mm above the vehicle sill, coinciding with the hip/thigh region of seated occupants. Supplementary bars are increasingly installed at shoulder and head height in premium models, creating comprehensive safety cages within doors.
Technical FAQ: Expert Insights
Q: What material advancements have transformed impact beam effectiveness?
A: The transition to press-hardened boron steels (22MnB5 grade) represents the most significant advancement. These ultra-high-strength steels achieve 1500-2000 MPa tensile strength after hot stamping and quenching processes, nearly triple traditional steel strength. Advanced coating systems like MagiZinc provide 20-year corrosion protection without compromising structural integrity.
Q: How do installation techniques affect collision performance?
A: Critical performance factors include end-bracket deformation geometry, with optimized crush initiators increasing energy absorption efficiency by 15-30%. Industry best practice mandates longitudinal positioning tolerance ≤ ±2.5mm and strategic gapping between beams and interior panels to prevent load path bypass during angular collisions.
Q: What are the main compliance testing protocols?
A: Manufacturers must comply with FMVSS 214 (US), ECE R95 (Europe), and GB 15743 (China) standards. Testing involves impactor collisions at 53km/h with measurements of thoracic trauma index (TTI), pelvic acceleration, and cabin intrusion. The latest Euro NCAP side pole test uses a 254mm diameter impactor at 32km/h, angled 75° to vehicle longitudinal axis.
Q: How does impact beam geometry affect safety performance?
A: Optimal tube diameter typically ranges 38-50mm, with wall thickness 1.8-3.0mm depending on strength requirements. Octagonal sections now show 12-18% superior resistance to diamond deformation modes compared to circular sections. Strategic crimping at beam ends enhances energy absorption by 25% without increasing weight.
Q: What innovations are shaping future systems?
A: Emerging technologies include hybrid aluminum-steel composite beams that reduce weight by 40%, and smart systems with piezoelectric sensors that stiffen structures milliseconds before impact. Mercedes-Benz is pioneering liquid-filled beams that harden upon collision detection through magnetorheological principles.
Technical References & Industry Research
- SAE International: "Structural Optimization of Automotive Door Impact Beams" - https://www.sae.org/publications/technical-papers/content/2020-01-0935/
- IIHS Research: "Side Impact Crashworthiness Evaluation Methodology" - https://www.iihs.org/topics/side-impact-protection
- Journal of Automotive Engineering: "Materials Science in Impact Protection Systems" - https://journals.sagepub.com/doi/10.1177/0954407019833297
- NHTSA Final Rule: FMVSS 214 Side Impact Protection - https://www.nhtsa.gov/document/fmvss-no-214-side-impact-protection-final-rule
- Euro NCAP Assessment Protocol - https://cdn.euroncap.com/media/58226/euro-ncap-assessment-protocol-2023.pdf
Engineering Safety Solutions
HEBEI CBIES AUTOMOTIVE PARTS CO., LTD.
Premium Door Impact Beam Tube Manufacturer Since 2010
Website: www.cbiestube.com
Product: Door Impact Beam Tube Solutions
✆ +86 311 6779 7385 | ✉ sales@cbiesautomotive.com
📱 +86 13572205873
🏭 No. 39 Xiangyi Road, Xinhua District, Shijiazhuang, Hebei, China